Table of Contents
- Balancing Budget and Quality in Necessary Orthopedic Supplies
- 3 Strategies For Better PPE Inventory Management
- 5 Cost-Saving Ideas for Your Healthcare Procurement Department
- How North American-Made PPE Protects Your Hospital From Supply Chain Disruptions
- Comparing PPE Solutions: What Purchasing Managers Need To Know
- Cost-Benefit Analysis: Why Hospitals Are Investing In High-Quality PPE
- Why Choose STA-DRI and ezGLIDE Products for Your Facility
- Protecting Healthcare Professionals for Over 35 Years
- Five Easy Ways to Order the Premium PPE You Need
Purchasing managers are the unsung heroes of the hospital. Your decisions regarding the supply of PPE and disposable medical clothing for the healthcare professionals in your facility can make a real difference in health and safety. After all, it’s your job to supply them with everything they rely on to keep them safe from bodily fluids, bloodborne pathogens, and illness.
Based on 30 years of experience protecting healthcare staff, with the added expertise of our founder, Urologist Dr. Stewart Sloan, and purchasing managers across the country, this is Sloan Medical’s Comprehensive Guide to Medical Supply Management.
Balancing Budget And Quality In Necessary Orthopedic Supplies
A purchasing manager’s job isn’t easy when it comes to balancing your budget versus the quality of necessary PPE supplies. You need to find the right products at the right price to provide the right protection for surgeons, staff, and patients in your facility.
Choosing products that are too expensive will bust your budget. Choosing products that are too cheap could risk bloodborne or fluidborne contamination and may even make people seriously ill.
Budget Challenges
Hospitals and surgical centers face several key budget challenges. Unpredictable economic fluctuations can hit hard. For example, a study from the American Hospital Association showed that many hospitals lost millions during the COVID-19 pandemic due to unexpected costs and changes in patient volume (AHA, 2020). Changes to reimbursement models can also create financial stress. When payment systems shift, hospitals may not get paid as they expect.
Labor shortages make these problems worse. With fewer healthcare workers available, hospitals must pay higher wages to attract staff. This leads to rising operational costs. These challenges strain financial resources. That’s why strategic financial planning is crucial.
Healthcare organizations need to control costs effectively and make proactive decisions to navigate these challenges. Budgeting is not just about numbers; it’s about planning for the future. Good financial planning can help hospitals stay afloat even when times are tough. With smart strategies, hospitals can better handle economic fluctuations, changes to reimbursement models, and labor shortages.
Quality Matters
Quality matters when it comes to personal protective equipment (PPE). Investing in premium products can make a big difference.
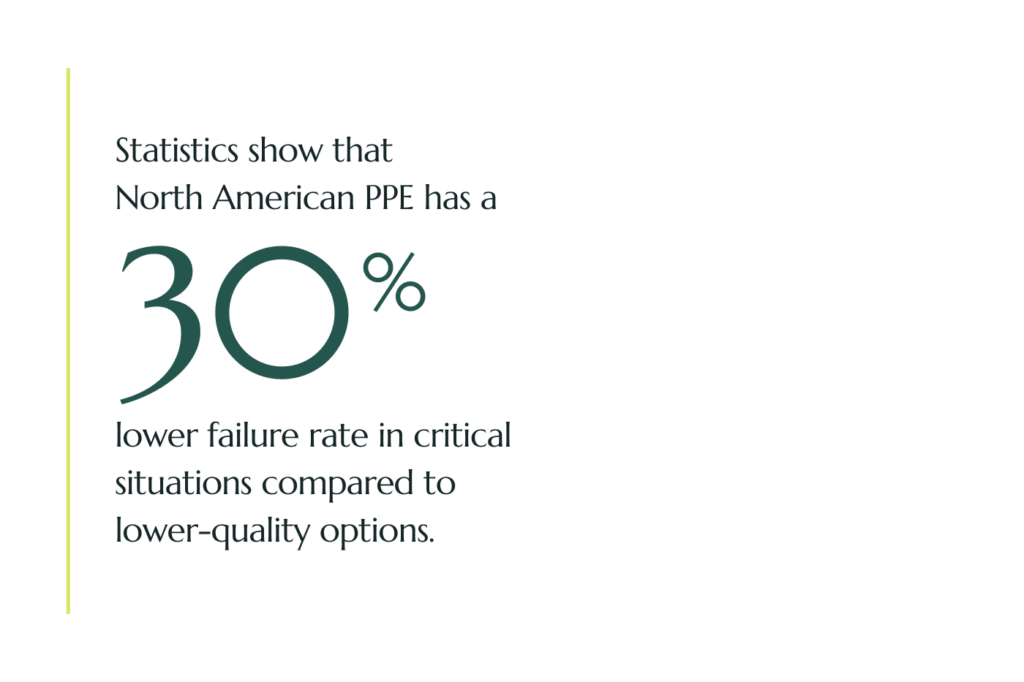
Statistics show that North American PPE has a 30% lower failure rate in critical situations compared to lower-quality options.
These manufacturers adhere to strict testing standards set by OSHA and ANSI, which ensure that PPE is made with high-quality materials and safe manufacturing processes.
The Balancing Act
When it comes to balancing your PPE budget, finding products that fall into the “Goldilocks Zone” is the best strategy. These products offer a perfect combination of high quality and moderate cost.
The Goldilocks Zone, to steal a phrase from our friends at NASA, refers to the “habitable zone” of a certain area. For your hospital, that habitable zone is where you get PPE products that are neither too cheap to be trusted nor too expensive to fit in your budget.
Balancing cost and quality becomes a top priority as you want to protect your surgical staff and patients without breaking the bank.
To ensure your selected PPE suppliers meet the necessary quality standards, request samples of their products. Evaluate the comfort, fit, and durability of the PPE firsthand. Additionally, verify that the products meet ASTM’s F1671 test standards for fluid impermeability.
Keep your staff & patients safe & dry (goodbye, squishy shoes!) with the tips in this blog!
3 Strategies For Better PPE Inventory Management
We all know the importance of proper PPE usage, and the pandemic reinforced it with a grave lesson – patients and staff are at an intolerable risk when PPE shortages hit critical facilities.
In the age of superbugs and with another pandemic only a “matter of time,” effective inventory management, especially for PPE supplies, is crucial.
Plus, efficient inventory management allows hospitals to control their costs by eliminating waste and overstocking. Maintaining reliable inventory levels optimizes the flow of supplies, ensuring that the right items are available when needed. This reduces time wasted searching for supplies or waiting for restocks, keeping staff supplied and patients safe.
Let’s take a look at three different inventory management strategies commonly used in healthcare: Just-In-Time (JIT) inventory management, Workflow/Trigger-Based Vendor Managed Inventory (VMI), and an innovative Disposable & One-Size PPE stocking strategy that can cut down on a lot of headaches. Naturally, all these strategies aim to enhance supply chain efficiency, reduce costs, and maintain adequate stock levels of critical medical supplies.
Just-in-Time (JIT)
Just-in-Time (JIT) inventory systems play a vital role in healthcare. They help organizations maximize operational efficiency. By reducing inventory levels, healthcare providers can minimize waste. This approach ensures that supplies arrive right when needed. For example, a study by the American Hospital Association found that JIT can reduce inventory costs by up to 30% (American Hospital Association, 2020).
However, JIT is not without risks. Strong supplier relationships are crucial for JIT to work effectively. If there’s a disruption in the supply chain, it can lead to shortages of critical supplies. For instance, during the COVID-19 pandemic, many hospitals faced challenges due to supply chain problems.
To implement JIT effectively, precise planning and coordination are essential. Healthcare providers need to forecast demand accurately. This helps ensure that they have the right products at the right time. JIT can bring great benefits to healthcare, but it requires careful management. Balancing efficiency and risk is key to success in JIT inventory management.
Vendor-Managed Inventory (VMI)
Vendor-Managed Inventory (VMI) is a smart way to manage supplies in healthcare facilities. With VMI, vendors watch the inventory levels closely using software systems and other triggers. They see when stock runs low and can restock items quickly. This helps prevent stockouts. It also avoids having too much inventory, known as overstock.
Real-time tracking is crucial in VMI. It allows vendors to see what is needed right away. When the system integrates smoothly, everyone benefits. Facilities can focus on patient care instead of worrying about supplies.
VMI strategies can lead to significant cost savings. Vendors save money by reducing waste. Facilities save money by not running out of supplies. A study by the Healthcare Supply Chain Association found that VMI can cut costs by 15% or more.
New Solutions: Disposables & One Size Fits
In today’s healthcare world, combining disposable solutions with one-size-fits-all technology can greatly enhance PPE management. One way to do this is by using disposable patient transfer sheets instead of traditional transfer boards. These sheets are easy to store and use. Plus, they help cut down on the risk of infection.
Using disposable transfer sheets means fewer items to track. This leads to reduced SKU (stock-keeping unit) management. Hospitals can save space in their storage areas. This space-saving is important in busy healthcare settings where every inch counts.
Moreover, these disposable options improve infection control. When healthcare workers use fresh sheets for each patient, the risk of spreading germs goes down. A study from the Journal of Hospital Infection found that using disposable items can reduce infection rates by up to 30%. By adopting disposable solutions, healthcare providers can ensure a cleaner environment for both patients and staff. In summary, moving to disposable patient transfer sheets offers a smart way to streamline PPE management while improving safety and efficiency.
5 Cost-Saving Ideas for Your Healthcare Procurement Department
Procurement and purchasing managers have it rough. Tasked with finding ways to save money without compromising on quality, safety, or patient care, your creative problem-solving skills are unmatched.
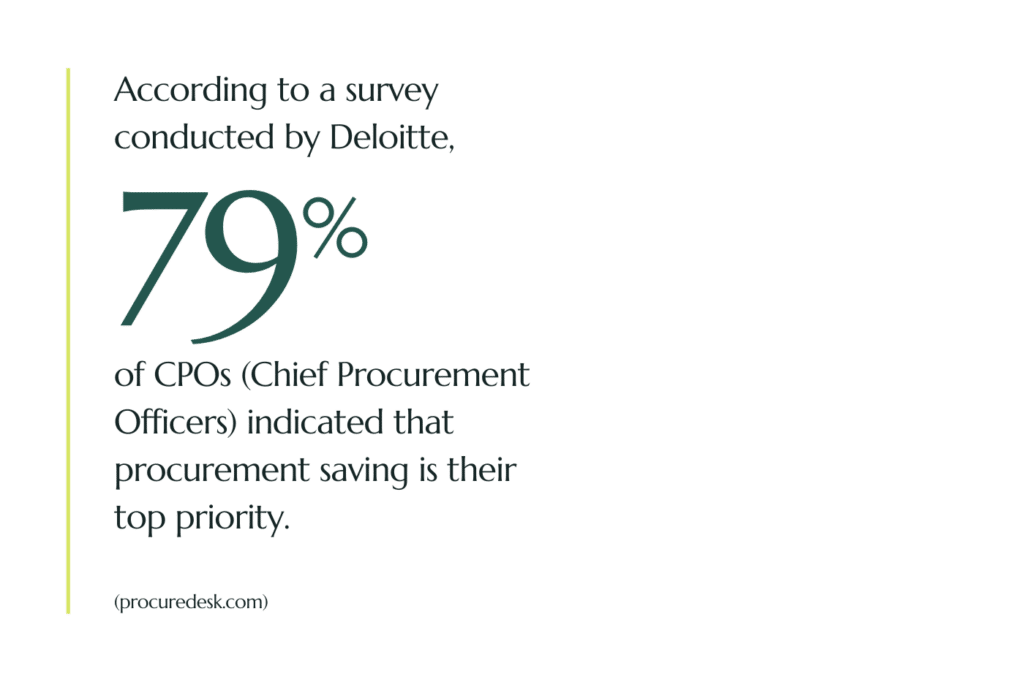
According to a survey conducted by Deloitte, 79% of CPOs (Chief Procurement Officers) indicated that procurement saving is their top priority. (procuredesk.com)
There are many out-of-the-box procurement strategies and cost-saving ideas out there, but we’ve narrowed the list down to the top five tips from our experience as both healthcare providers (thanks to our founder’s experience as a urologist) and healthcare suppliers.
Cost Avoidance
Cost avoidance is essential in healthcare procurement. It helps keep expenses down while maintaining high-quality care. One key strategy is contract management. Reviewing contracts ensures organizations get the best terms and prices. For example, regular audits can save healthcare facilities 1-2% annually (Source: MedAssets).
Another smart approach is using data analytics. By analyzing spending patterns, organizations can spot wasteful expenses, which lets them make informed decisions. For instance, data can highlight overpriced supplies, allowing adjustments to save money.
Collaboration with other healthcare organizations also aids in cost avoidance. When group purchasing is used, members benefit from lower prices due to bulk buying. This strategy can cut costs by around 10-20% (Source: Vizient).
Inventory management plays a critical role, too. By tracking supplies closely, organizations can avoid overstocking and waste. Lastly, value analysis helps assess the cost and quality of products. This ensures that every dollar spent delivers great care.
Cost Savings
Healthcare facilities face rising costs for personal protective equipment (PPE). To achieve cost savings, they can use smart strategies during PPE procurement. First, evaluating suppliers is crucial. Facilities should compare prices, reliability, and quality from various vendors. This ensures they get the best deals.
Next, purchasing in bulk can help. Buying larger quantities often lowers the price per item. For example, a hospital could save 15% or more by ordering in bulk. This can lead to significant savings over time.
Lastly, optimizing inventory management is important. Facilities can track PPE usage to avoid overstocking or running out of supplies. Using inventory software can help manage stock levels efficiently, preventing waste and reducing unnecessary expenses.
Cash Flow Savings
Managing cash flow is crucial for any business, especially when it comes to sourcing personal protective equipment (PPE). By sourcing PPE locally, companies can optimize their inventory practices. This approach reduces storage costs while ensuring a secure supply chain. When you source PPE near your location, shipping times are shorter. This means products arrive faster.
Using the “just in time” inventory method allows businesses to receive supplies only when needed. This method helps maintain flexibility and control over cash flow. According to a study by the Supply Chain Management Review, companies can reduce inventory costs by up to 50% by using this approach.
Moreover, these strategies protect against supply shortages. With a steady local supply of PPE, companies face fewer disruptions. This leads to smoother operations and cost savings. In conclusion, focusing on local sourcing for PPE not only enhances cash flow but also strengthens overall business performance. By keeping your supply chain efficient and adaptable, you can navigate challenges more effectively.
Value-Based Procurement (VBP)
Value-Based Procurement (VBP) is a way to buy goods and services based on the value they provide. Instead of just looking at costs, VBP focuses on how these goods and services improve patient outcomes. This means healthcare providers want to buy products that help patients get better and stay healthier.
One key principle of VBP is aligning incentives with outcomes. This encourages everyone to work towards the same goals. For example, if a hospital buys a new medical device that helps patients recover faster, both the manufacturer and the hospital benefit. They both want to see good results.
Collaboration among stakeholders is also important in VBP. It involves working together to make the best choices for patients. When hospitals, doctors, and suppliers communicate effectively, they can share ideas and find solutions that improve resource allocation. This means they can use resources wisely, cutting down on unnecessary healthcare costs while still providing great care.
By focusing on value instead of just price, VBP has the potential to change how healthcare is delivered. It leads to better results for patients and healthier communities.
How North American-Made PPE Protects Your Hospital From Supply Chain Disruptions
Hospitals all over the United States struggled to get the PPE they needed during the COVID-19 pandemic. In the aftermath, it became clear to most suppliers and hospital purchasing managers alike that relying on foreign manufacturers comes with that risk.
Health officials are already watching 8 diseases that could create the next pandemic. The Harvard School of Public Health says that it’s just a matter of time before the world is back in the hot seat.
Can U.S. hospitals and PPE suppliers be better prepared this time?
What the pandemic taught us about reshoring manufacturing
The COVID-19 pandemic highlighted the weaknesses in global supply chains. Many countries faced shortages of personal protective equipment (PPE). Hospitals couldn’t get enough masks, gloves, and gowns. This problem forced companies to rethink manufacturing methods – and locations. As a result, many businesses started “reshoring” or bringing production back to their own countries.
Bringing production closer to home has clear benefits. First, it creates job opportunities. When factories open locally, they hire workers from the community. Second, it improves response times. Local production means faster access to important supplies like PPE. Lastly, it reduces shipping risks. With fewer delays, hospitals can get the supplies they need quickly.
Why buy PPE from North American manufacturers?
When it comes to buying PPE, choosing North American manufacturers brings many benefits. First, it often saves money. Local production cuts shipping costs and reduces delays.
Quality is another crucial factor. North American manufacturers, like Sloan Medical, follow strict standards. Wherever your PPE is manufactured, it should meet the ASTM-F1671 testing standard for fluid impermeability. Quality PPE is vital for keeping workers protected.
Another advantage is rapid shipping. Companies like Sloan Medical can deliver products quickly. This helps protect cash flow and keeps your supply chain resilient. You won’t have to worry about running out of essential equipment, but you can still buy “just enough” instead of stocking a surplus.
Purchasing managers also often find that ordering PPE from North American manufacturers is a more consistent, easier process. You can pick up the phone or send a simple email with questions or urgent needs, and your North American partner will be on the same day, time, and wavelength.
The PPE products themselves are also more consistent from North American sources. These manufacturers follow strict quality standards. They often have better oversight of their production processes. For instance, a survey found that 85% of buyers prefer PPE made in North America due to its reliability.
See how the new North American PPE supply chain can benefit your hospital, patients, and community.
Comparing PPE Solutions: What Purchasing Managers Need To Know
When purchasing managers choose personal protective equipment (PPE) for their hospital or healthcare facility, they’re making a big decision. The U.S. healthcare industry, which employs over 22 million workers, has one of the highest rates of nonfatal work injury and illness in the country.
In 2020, there were 78,740 cases of nonfatal workplace injuries and illnesses that resulted in at least one day away from work among registered nurses in private industry. This was a 290.8-percent increase, about four times as many cases, compared with 2019, when there were 20,150 such cases.
And that’s just RNs. There were hundreds of thousands of other injuries and sick days taken for the rest of the healthcare teams across the industry. High-quality PPE is the first line of defense, so make sure you’re comparing your options.
How to select PPE for protection against pathogens
Selecting the right personal protective equipment (PPE) is crucial to prevent infections in healthcare settings. When choosing PPE, consider the material, fit, durability, comfort, and accessibility.
The material quality affects how well the gear blocks pathogens. For example, gowns made of fluid-resistant materials protect against splashes. The fit is also important. If PPE is too loose, it may not provide adequate protection. Durable equipment lasts longer, which saves money and reduces waste.
Comfort matters, too. Healthcare workers often wear PPE for long shifts. If the gear is uncomfortable, it may distract them from their tasks. Accessibility is key as well. Easy-to-find PPE ensures that it can be worn quickly when needed.
Standards & specifications
Organizations like OSHA, NIOSH, ASTM, and AAMI set important guidelines and standards for PPE use and manufacturing. You’ll want to make sure the PPE you select passes the standardized tests and meets the requirements set by these agencies.
For example, ASTM standards classify protective clothing into levels based on their barrier performance. Levels 1 through 4 indicate how well the clothing protects against fluids and pathogens. Levels 2 and 3 are particularly important for surgical use. They ensure that gowns and gloves resist liquid penetration, keeping both patients and staff safe.
Reusable garments versus disposable medical protective clothing
There are two main types of medical protective clothing: reusable PPE and disposable PPE. Each type has different materials, uses, and levels of protection. Reusable PPE is made from durable fabrics that can be washed and used again. It’s great for low-risk tasks.
On the other hand, disposable PPE is made from lightweight, fluid-impermeable materials. This type is meant for higher-risk situations. Since it’s used just once, it helps simplify infection control. Throwing it away after a single use reduces the chance of cross-contamination.
It’s important to consider environmental impact, too. Reusable PPE may reduce waste in the long run, but it requires energy and resources for cleaning. Disposable PPE, while convenient, does create waste.
The hidden costs of reusable PPE garments
Many people think that reusable PPE garments, like certain gowns, save money. However, there are hidden costs involved.
First, washing and maintenance can be expensive. According to the American Journal of Infection Control, these costs can add up quickly. Facilities must wash these gowns often to keep them safe and clean. This means spending on water, detergent, staff, and energy.
Second, replacement and repair can also be costly. Reusable PPE may need fixing or replacing sooner than expected. This adds extra costs that some may not plan for.
Lastly, inventory management can pose challenges. Keeping track of clean and dirty garments takes time and money. It can lead to overstocking or understocking, both of which impact budgets.
In fact, that study by the American Journal of Infection Control shows that reusable gowns can have a higher cost per use compared to disposable options. These extra costs come from washing, repairs, and storage. Always consider these hidden costs when choosing PPE for your facility.
Get the details and a link to our comprehensive comparison guide in this article.
Cost-Benefit Analysis: Why Hospitals Are Investing In High-Quality PPE
After the COVID-19 pandemic, more hospitals are shifting away from cheaper PPE options and investing in high-quality gear.
Although premium PPE may be more expensive upfront, it also reduces costs in the long run. Better PPE means fewer infections, fewer staff sickouts, less cross-contamination, and shorter hospital stays for patients.
By investing in high-quality PPE, hospitals can reduce illness among staff. Studies show hospitals that use top-tier PPE see a 50% decrease in infection rates compared to those that use lower-quality options (Source: CDC). Let’s examine the cost-benefit analysis of high-quality PPE, and you’ll see that safety and savings can go hand in hand in your hospital, too.
The High Price of Low-Cost PPE Options
Many healthcare facilities find low-cost PPE options tempting. They promise big savings on expenses like masks, gowns, and gloves. However, these options can come with hidden dangers. Low-cost PPE often lacks the quality needed to protect healthcare workers, leading to increased risks of injuries and illnesses.
When PPE fails, the effects can be severe. Healthcare workers may get sick or injured on the job, which affects their health and the hospital. Studies show that poor-quality PPE can cause a rise in employee turnover rates. When workers feel unsafe, they’re more likely to leave. According to the Bureau of Labor Statistics, turnover in healthcare can cost up to $4.4 million a year for a 200-bed facility.
These hidden costs add up quickly. Hospitals may face additional staffing costs if they need to hire new workers, and they may also see lower employee satisfaction. In the end, saving money on low-cost PPE can lead to bigger financial problems. Investing in high-quality PPE ensures safety for healthcare workers and saves money long-term.
Your Hospital’s Return on Investment
Investing in high-quality PPE (personal protective equipment) actually leads to a significant return on investment for hospitals. First, durable PPE fails or rips less often, reducing the need for frequent replacement or “double dipping” by your staff. This saves money over time. For example, a study by the American Hospital Association found that stocking more durable PPE can lower costs by 23% over five years.
High-quality PPE also improves worker productivity. When staff feel safe, they can focus on their jobs. When workers are well-protected, there’s a lower risk of spreading infections from patient to patient.
As a result, hospitals see reduced medical expenses and shorter hospital stays. A cost-benefit analysis shows that investing in high-quality PPE can lower overall costs by nearly 12%.
Calculating the Cost of Premium PPE Investments
Calculating the cost of premium PPE investments involves looking at both initial costs and long-term savings. Healthcare purchasing managers must consider how these costs impact operations. While premium PPE may seem expensive upfront, it can lead to significant savings later.
According to the Centers for Disease Control and Prevention (CDC), high-quality protective gear can reduce infection rates by up to 30%.
This reduction in infections not only helps patients but also decreases staff sickouts. When healthcare workers stay healthy, operational efficiency and patient care are improved. Fewer staff absences mean more hands on deck, leading to better service for patients.
Moreover, premium PPE can shorten patient hospital stays. The financial benefit is clear—shorter stays free up resources and cost less overall. A cost-benefit analysis shows that investing in high-quality PPE can save healthcare facilities money in the long run.
See more factors for your cost-benefit analysis and how to calculate the return on investment here.
Why Choose STA-DRI and ezGLIDE Products for Your Facility
When it comes to choosing products for your facility, STA-DRI and ezGLIDE® from Sloan Medical offer exceptional options for keeping staff and patients safer.
Lab Tested, Surgeon Approved
At Sloan Medical, we take pride in providing top-quality products that meet the highest standards of impermeability. All our disposable wearables have passed the ASTM F1671 testing process and standards.
ASTM International, formerly known as the American Society for Testing and Materials, is an international standards organization that develops and publishes voluntary consensus technical standards for a wide range of materials, products, systems, and services.
The ASTM F1671 test methods evaluate the effectiveness of protective barriers against penetration by bloodborne pathogens. This rigorous evaluation process ensures that our products meet the utmost safety standards.
Sloan Medical manufactures surgical apparel and medical-grade disposable garments that meet ASTM’s F1671 test standards for impermeability, ensuring the full protection of your staff and patients.
View our ASTM SDOC Materials Testing Approval
By Healthcare Professionals, For Healthcare Professionals
Involving surgeons and other medical professionals in the process of creating new types of personal protective equipment (PPE) is core to the way Sloan Medical develops and improves our products.
Surgeons will use this PPE daily in potentially high-stress and intense environments. Their expertise and insights are invaluable when it comes to ensuring that the equipment meets their specific needs and requirements. Purchasing managers like you have also helped us inform how, when, and where we sell our products.
Over the years, Sloan Medical has spoken to thousands of end users and partnered with dozens of them to remain connected to the needs of his fellow medical professionals.
“Truly, the key difference is we listen to our customers. Always have, always will. We respond to feedback with solutions and enhancements, and I am usually the one talking to them myself. It’s important to understand what they’re trying to accomplish, their goal, or their problem. That’s why they trust us.”
—Stewart Sloan, Founder
Get to know Dr. Stewart Sloan! Read the full interview and profile here.
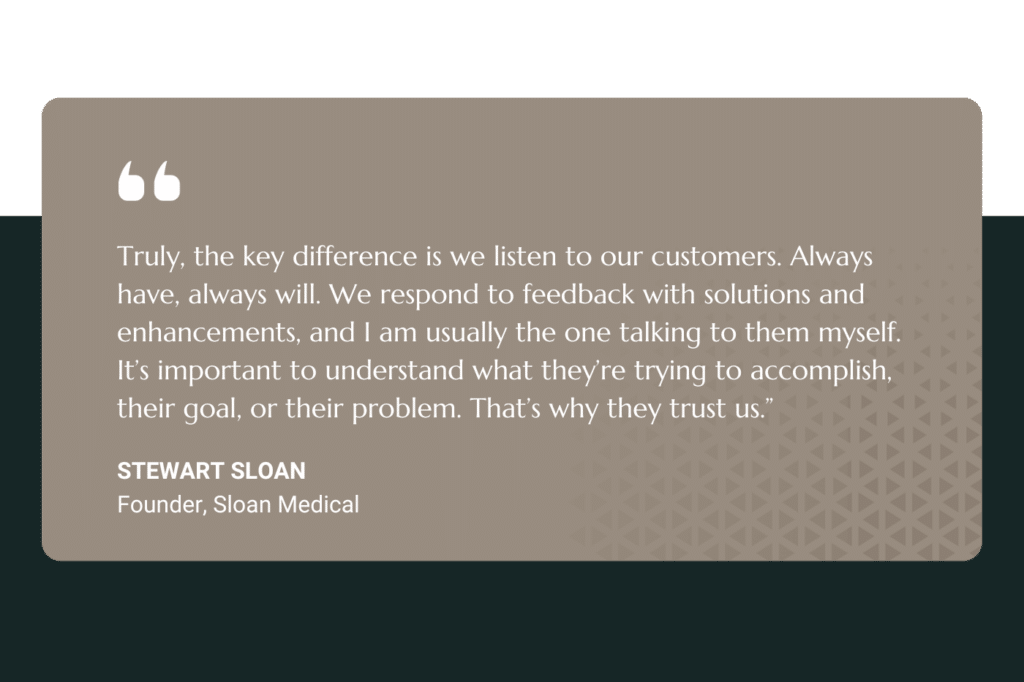
Protecting Healthcare Professionals for Over 35 Years
At Sloan, we make four promises to every customer:
Guaranteed to keep you safe and dry: You won’t sweat the wet. We’ve designed, tested, and continually improved our products to ensure that they do their job—so you feel confident doing yours.
One-size-fits-all reduces inventory: Save shelf space. Your entire team is protected with covers that easily fit any size—and can be restocked with a single SKU.
Personalized service: No need to demand an account “representative.” Our Midwest-based, family-owned company was founded by a urologist who treasures personalized service.
Handcrafted in North America: With products made in North America, you can eliminate overseas delays and keep PPE readily available for your team. Most products ship within 24 hours.
Explore the full catalog & save this order form!
Five Easy Ways to Order the Premium PPE You Need
We offer five easy ways to order our products so that your workflow continues uninterrupted and you get the best PPE on the market in the hands of your healthcare staff within days! Sloan Medical takes pride in shipping all direct orders within 24-48 hours to keep our partners and customers well-stocked, safe, and dry.
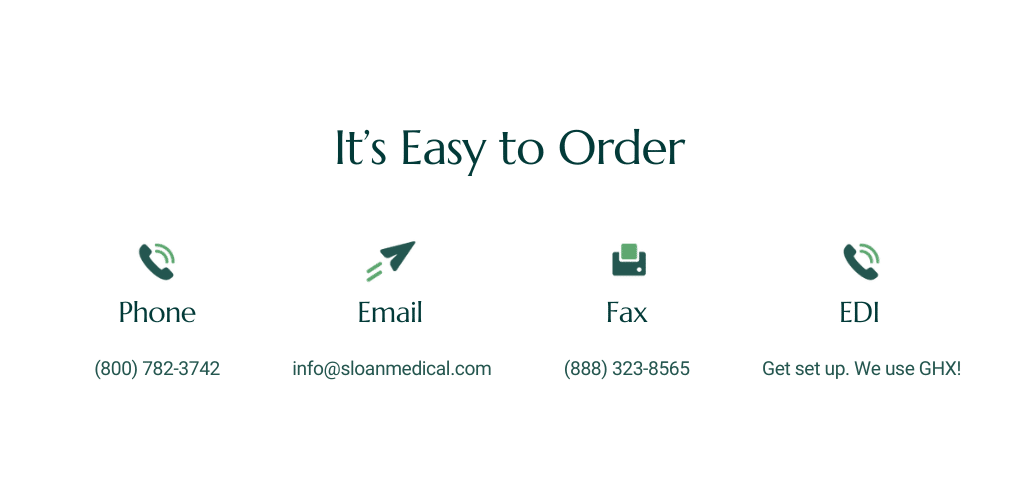
Ordering Through Distributors
Sloan Medical products from our STA-DRI and ezGLIDE® lines are stocked by most of the nation’s top distributors. Order your Sloan products from:
Bowers Medical Supply
Bowers Medical Supply is dedicated to providing excellent healthcare products and solutions, focusing on quality, affordability, and exceptional customer service.
Buffalo Hospital Supply
Buffalo Hospital Supply offers a comprehensive selection of medical equipment and supplies. From surgical instruments to patient care products, they have everything you need to facilitate effective and efficient healthcare delivery.
Cardinal Health
As a global, integrated healthcare services and products company, Cardinal Health plays a pivotal role in delivering essential solutions to patients, healthcare providers, and manufacturers worldwide. With a strong commitment to improving the quality and efficiency of healthcare, Cardinal Health has become a trusted partner in the industry.
Concordance Healthcare Solutions
Concordance Healthcare Solutions is one of the largest independent, regional healthcare distributors in the U.S. Concordance offers products like Sloan Medical’s full suite of options. Concordance Healthcare Solutions serves nursing homes, hospitals, physician practices, labs, government facilities, home care, hospice, healthcare education, and redistribution businesses.
Healthmark Industries
Healthmark Industries is a leading provider of innovative solutions for healthcare professionals. With a deep understanding of the challenges faced in healthcare settings, Healthmark Industries is dedicated to developing products and services that promote safety, efficiency, and compliance.
LeeSar / Cooperative Services of Florida
LeeSar is a cooperative purchasing and supply chain management organization. By pooling the purchasing power of its member healthcare facilities, LeeSar negotiates contracts with suppliers to secure the best possible prices for medical supplies, equipment, and services. This allows member facilities to save money and allocate resources more effectively.
McKesson
With an extensive presence across the United States and around the globe, McKesson serves as a vital link, connecting manufacturers, healthcare providers, and patients through a seamless and secure supply chain. By leveraging its scale and expertise, McKesson plays a pivotal role in safeguarding the availability of vital medications for countless individuals worldwide.
Medline Industries
Medline Industries is a leading healthcare company that has been serving the needs of the medical community for over 100 years. Founded in 1910, Medline has grown to become one of the largest privately held manufacturers and distributors of medical supplies and equipment in the United States.
Owens & Minor
As a leading global healthcare solutions provider, Owens & Minor delivers innovative and reliable solutions like ours to hospitals, clinics, and other healthcare facilities. With a deep understanding of the challenges faced by healthcare providers, Owens & Minor is dedicated to helping them improve patient outcomes and reduce costs.
Professional Hospital Supply
Professional Hospital Supply is a trusted partner in meeting the healthcare community’s medical supply needs. With a comprehensive range of products, fast shipping, and a commitment to quality and affordability, many facilities stock their PPE products through PHS.
Shared Service Systems
Shared Service Systems offers medical/surgical supply distribution services in Iowa, Nebraska, Missouri, and Kansas from their 100,000-square-foot distribution center in Omaha, Nebraska.
EDI via GHX
Ordering Sloan Medical products through GHX using your existing EDI is a simple and efficient process. Here’s a step-by-step guide to help you get started:
- Firstly, access your existing EDI system and log in with your credentials.
- Navigate to the GHX platform within your EDI system.
- Once within GHX, search for Sloan Medical as your preferred supplier.
- Select the desired Sloan Medical products from their extensive catalog.
- Add the selected items to your cart and review your order.
- Verify the order details, including quantities, pricing, and shipping information.
- Proceed to the checkout process and confirm your order.
- GHX will automatically generate an electronic purchase order (PO) and send it directly to Sloan Medical.
- Sit back and relax as Sloan Medical receives your order and initiates timely processing.
Our support staff is happy to help you set up your EDI to order our products. The setup is quick and easy, and you can schedule any time that works best for you!
Direct by Phone
Ordering directly by phone is a convenient and efficient way to get the products and services you need. Here at Sloan Medical, we understand that some customers prefer the personalized touch of speaking to a real person when placing orders.
Reference this order form and call us at (800) 782-3742.
Direct by Email
Did you know that you can easily order our products through email? It’s as simple as sending your request to info@sloanmedical.com.
Just use this digital order form, fill in the quantities you need, and send us an email.
Direct by Fax
To place your order by fax, print this order form, jot down the quantities and products you want to purchase, and then fax it to (888) 323-8565.
Amazon
You can now conveniently order small quantities of Sloan Medical STA-DRI Knee Highs on Amazon.
Of course, if you’d like to try the product, we’re happy to send you a free sample package!
Buying Premium PPE From a North American Manufacturer Pays Off
As you make the shift to premium PPE, consider Sloan Medical for your shortlist. Our product lines have been perfected over our 30+ years in business and are guaranteed to perform in all types of environments.
With all our products handcrafted in North America and tested against the ASTM-F1671 standard, we do not cut corners when it comes to protecting medical professionals.
You can order exactly what you need when you need it and protect your cash flow. Our Midwest-based, family-owned company genuinely treasures the healthcare community and values personalized service.